An expert explains what safety features a submersible should have
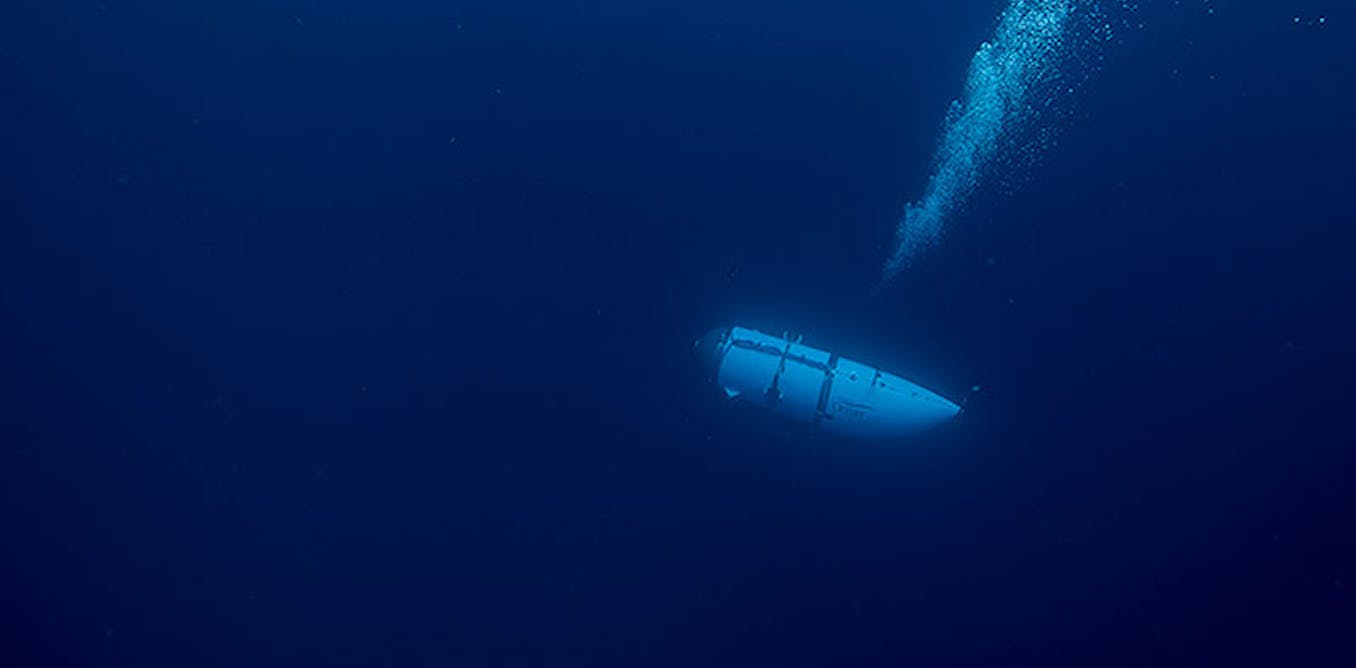
The oxygen supply of the missing Titan submersible is expected to run out today around 10am GMT, or 8pm AEST.
A frantic search continues for the Titan and its five occupants, with sonar buoys having recorded “banging” noises in the search area on Tuesday and Wednesday.
With the vessel’s fate yet to be determined, the general public is asking questions about the safety of such touristic endeavours.
Read more: Missing Titanic sub: what are submersibles, how do they communicate, and what may have gone wrong?
The context
The context in which the Titan has disappeared is disturbing. Reports have come out detailing court documents from a 2018 case that show OceanGate, the company responsible for the Titan, fired employee David Lochridge after he expressed concerns about the submersible’s safety.
Lochridge disagreed with OceanGate about the best way to demonstrate the asset’s seaworthiness, and objected to OceanGate’s decision to perform dives without prior “non-destructive testing” to the vessel’s hull to prove its integrity.
Also in 2018, a letter sent to OceanGate by the Manned Underwater Vehicles Committee of the Marine Technology Society, signed by 38 experts, expressed reservations about the submersible’s safety. They said the “[…] experimental approach adopted by OceanGate could result in negative outcomes (from minor to catastrophic) that would have serious consequences for everyone in the industry”.
As we can see from these exchanges, the engineering and regulation of deep-sea submersibles remains somewhat uncharted territory. And since the Titan operates in international waters, it is technically free from governance by any single nation’s regulations.
In this case, most submersible designers would elect to have a classification society certify the vessel’s design. OceanGate made the conscious decision to refuse to do this for the Titan.
Seaworthiness of submersibles
When we talk about the “seaworthiness” of a marine vessel, we are essentially asking if it is fit for purpose, safe to operate, and compliant with the protection of the environment.
For the Titan, fitness for purpose could be summarised by the ability to safely launch from a mothership on the water’s surface, operate autonomously down to 4,000m (the approximate depth of the Titanic shipwreck), and resurface for recovery by the mothership after a dive of a few hours.
Safety to operate would mean no equipment is damaged and no passengers are prone to injury (or worse) while onboard. And protection of environment means the submersible would not have any significant impact on its surroundings, such as through pollution or disturbing the ecosystem.
However, this is the blue-sky scenario. Deep-sea submersibles operate in a hostile environment, and things can go wrong.
Pressure resistance
Submersibles and submarines are shaped the way they are because spheres and cylinders are geometrically more resistant to crushing pressures.
Instead of operating in a breathable atmosphere of 1 bar, the Titan would have to withstand 370 bars of pressure in seawater at the depth of the Titanic. Any defect in the hull could result in instantaneous implosion.
So what is the threshold below which an “out-of-circularity” geometry becomes a defect?
Industries using underwater vessels at depths of a few hundred metres will often use steel hulls, which usually have an out-of-circularity threshold below 0.5% of the vessel’s diameter. Would that criterion be safe enough for the pressure hull of the Titan at 4,000m?
The Titan is made of a composite carbon fibre-titanium hull. It is extremely complicated to design and structurally assess these materials, compared to metallic material only. One can assume this is why OceanGate equipped the Titan with a “real-time hull health monitoring system”.
It’s unclear if the system actually measures the stresses with strain gauges in the hull, or if it is (as Lochridge warned) an acoustic analysis that would only alert people about imminent problems “often milliseconds before an implosion”.
Safety for pressure hull integrity requires analysing various failure modes, before determining a safety coefficient for each mode, depending on the deep diving depth aimed at.
After the design is verified (through calculations), real-world validation should occur in two steps.
Non-destructive testing should be done on the manufactured pressure hull, to check the preciseness of its geometry and any out-of-circularity aspects.
Then, actual dives (ideally unmanned) should be carried out at progressively increasing depths, with stress gauges used to measure actual values against predictions. We don’t know whether the Titan underwent such tests.
Back-ups and redundancy
In designing the functional architecture and selecting equipment, a designer would consider a number of “what if” scenarios to recover from:
- what if main power sources fail?
- what if my computer crashes and the pilot loses control?
- what if my main communication system fails?
- how can the submersible signal to the mothership there is a problem?
These scenarios commit the naval architects to ensure what’s called a safety SFAIRP (so far as is reasonably practicable). This involves not only mitigating the consequences of an accident, but also preventing it from happening.
In practical terms, it means having:
- a reserve of oxygen (such as while waiting for a rescue party)
- reliable main power sources and back-up systems
- another power source (such as hydraulic) in case of power loss – this would help, for example, to release safety leads to get positive buoyancy and rise back to the surface.
Each of these systems would need a specific verification (theoretical) and validation (tests) for the specific environment.
Commercial off-the-shelf equipment can potentially fit onboard, if a demonstration of fitness for purpose is made for various scenarios. However, most of the external components (because of crushing pressure) and safety systems would warrant custom design.
According to reports, the Titan was using certain “off-the-shelf” equipment, but it’s difficult to say whether this was certified for its intended use at these depths.
Safety systems
In the Titan’s case, a tether with the mothership would have ensured instant two-way communication and a higher data exchange rate. But these cables can get entangled with potential hazards at a shipwreck site.
As such, tethers are mostly used for unmanned vehicles; manned submersibles prefer to trust the pilot. Also, GPS, portable satellite phones and automatic identification systems can’t be used underwater. These tools use electromagnetic waves that don’t propagate deep underwater (although they could be used on the surface).
Some submarines are equipped with a distress beacon, the equivalent of an emergency position indicating radio beacon (EPIRB). This can be released at the captain’s order, or via a “dead-man” switch; if the pilot responds to a test at regular intervals, a sudden lack of response leads the system to assume the crew is incapacitated.
Hopefully, the “banging” sounds that have been reported are the Titan’s crew and passengers banging against the pressure hull every 30 minutes. This is a technique taught to military submarine crew when grounding on the sea floor.
A high-frequency acoustic pinger would be even more efficient, as this would provide directional accuracy to home onto a distressed submersible.
There are a number of situations that can unfold on the surface too, in the case that the Titan has floated its way up. Even if has (or will do so), the crew and passengers can’t open the vessel’s bolted hatch. They would likely have to continue to contend with the potentially fouled atmosphere inside.
Further complicating matters is the Titan’s white colour, which would make it harder to spot in the foaming sea. This is why floating assets detected from above are usually in orange or yellow shades allowing higher visibility.
The future of deep-sea submersibles
Hopefully, the crew and passengers of the Titan will be rescued. But if the worst happens, forensic examination will inevitably look into whether the Titan met the basic thresholds to demonstrate seaworthiness.
Although various classification societies propose a set of rules for commercial submarines and submersibles, opting to follow these rules remains a voluntary process (which the asset’s insurer usually pushes for).
It’s time to acknowledge that going deep is as complex, if not more complex, than going into space – and that ensuring the safety of submersibles ought to be more than a matter of choice.